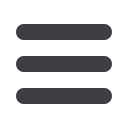
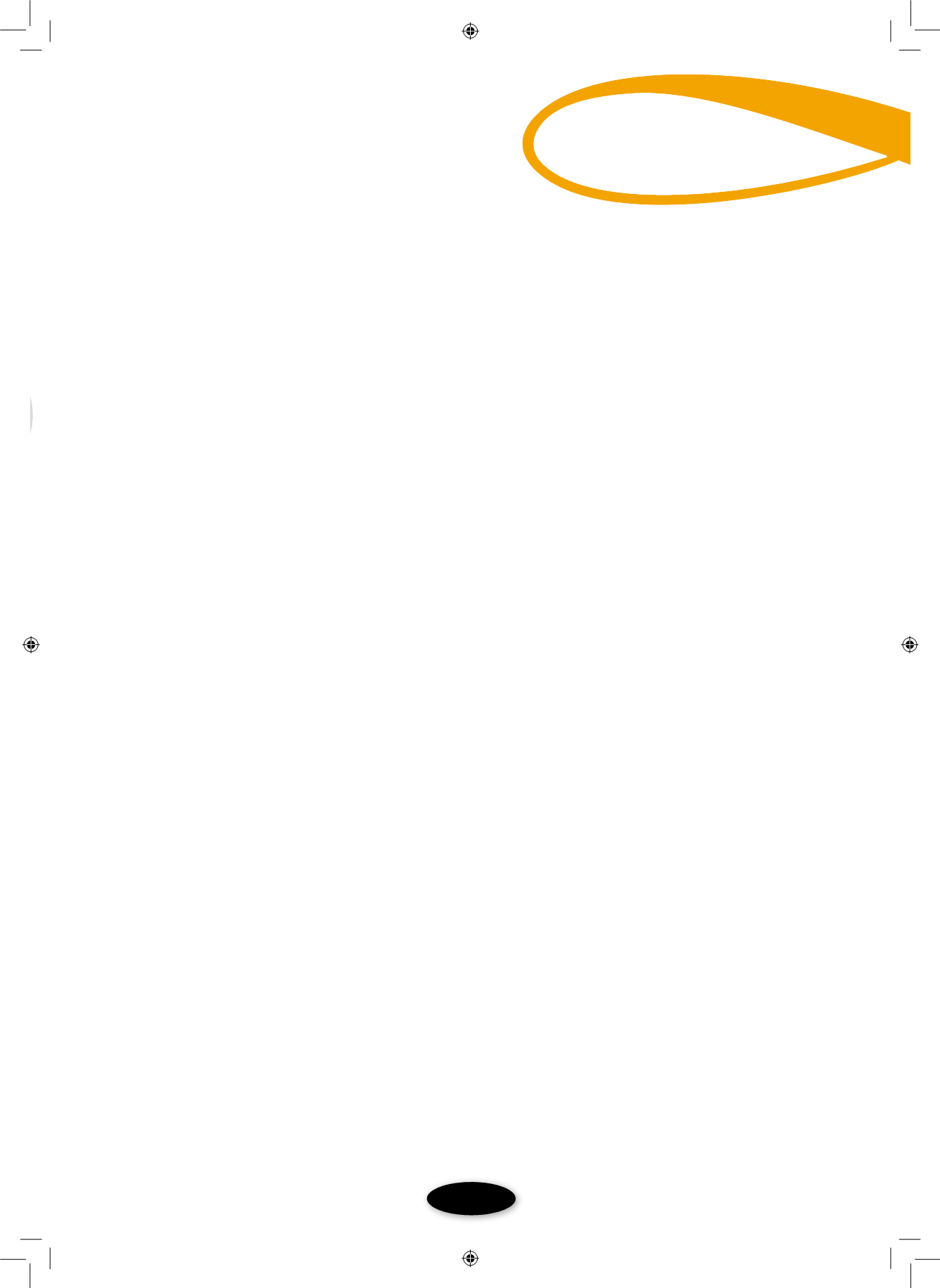
11
Chairman’s Communiqué
promoted from the Americas. He believed he could
produce a better machine and block and in 1988 took the
plunge to invent it. While Elmarie Kofahl concentrated
on her job at the bank, Jochen started operations in their
Boksburg garage. He soon cajoled Robert into giving up
his job and together they worked on the dream, operating
on the slimmest of funds.
Disappointments were regular and their first major
demonstration before a raft of professionals was an
unmitigated disaster, with oil flooding the yard and
themselves as they sought to rectify problems. But
gradually they surmounted challenges and by the time
of my initiation they had made substantial strides, having
developed reasonable machines and the now common
220mm block norm. They had also established the name
Hydraform.
While Robert concentrated on selling, Jochen
demonstrated a flair for developing and inventing while
involving knowledgeable academics, professionals and
businessmen to help with technical, legal and attitudinal
roadblocks and to increase acceptability of Hydraform’s
“soil-cement” block concept in South Africa and beyond.
Their efforts took them through the various South African
institutes with extensive testing and work at the Council
for Scientific and Industrial research (CSIR), the South
African Bureau of Standards (SABS), and the University
of the Witwatersrand (Wits) where eventually Hydraform
became part of three faculties’ syllabi and from where a
number of Hydraform executives have been sourced. This
led to Hydraform’s Agrément Certificate – an essential for
building approval in South Africa and across Africa.
By the early 1990s steps were being made to other
African countries besides Malawi with marketing and
technical exercises carried out across Africa, in India and
in South America. All this was done by a tiny team on the
smallest of budgets.
Major advantages were recognised in the mobility
of Hydraform machines to the most remote of sites,
the reduced use and cost of cement, reduced cost of
transport, the ease of operation with previously unskilled
labour, the high-quality standard block shape and face-
brick potential, the elimination of tree-felling for clay-brick
burning, the use of non-specialist sub-soils, and the host
of other advantages in this eco-friendly and economical
process, now almost taken for granted.
Myriad problems were also tackled, from copying of the
machines against patent and trademark rights to political
manipulation and obstruction, as well as sloppy processing
and management at many sites causing unacceptable
building quality failures.
Now Hydraform is both a household name and a generic
for soil-cement blocks and systems. After all the years
of hard work and innovation we are firming our grip on
processes and training to move up a gear into the growing
soil-cement market.
So after 25 years we are the target and not the
newcomer, but this does not faze us – rather it pushes us
to keep ahead of the copycats with continued innovation,
quality and training support.
The past has been full of challenges overcome and the
future is an opportunity to embrace.
JHM Carter
Chairman
Hydraform3.indd 11
6/18/13 11:39 AM