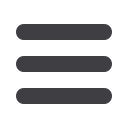
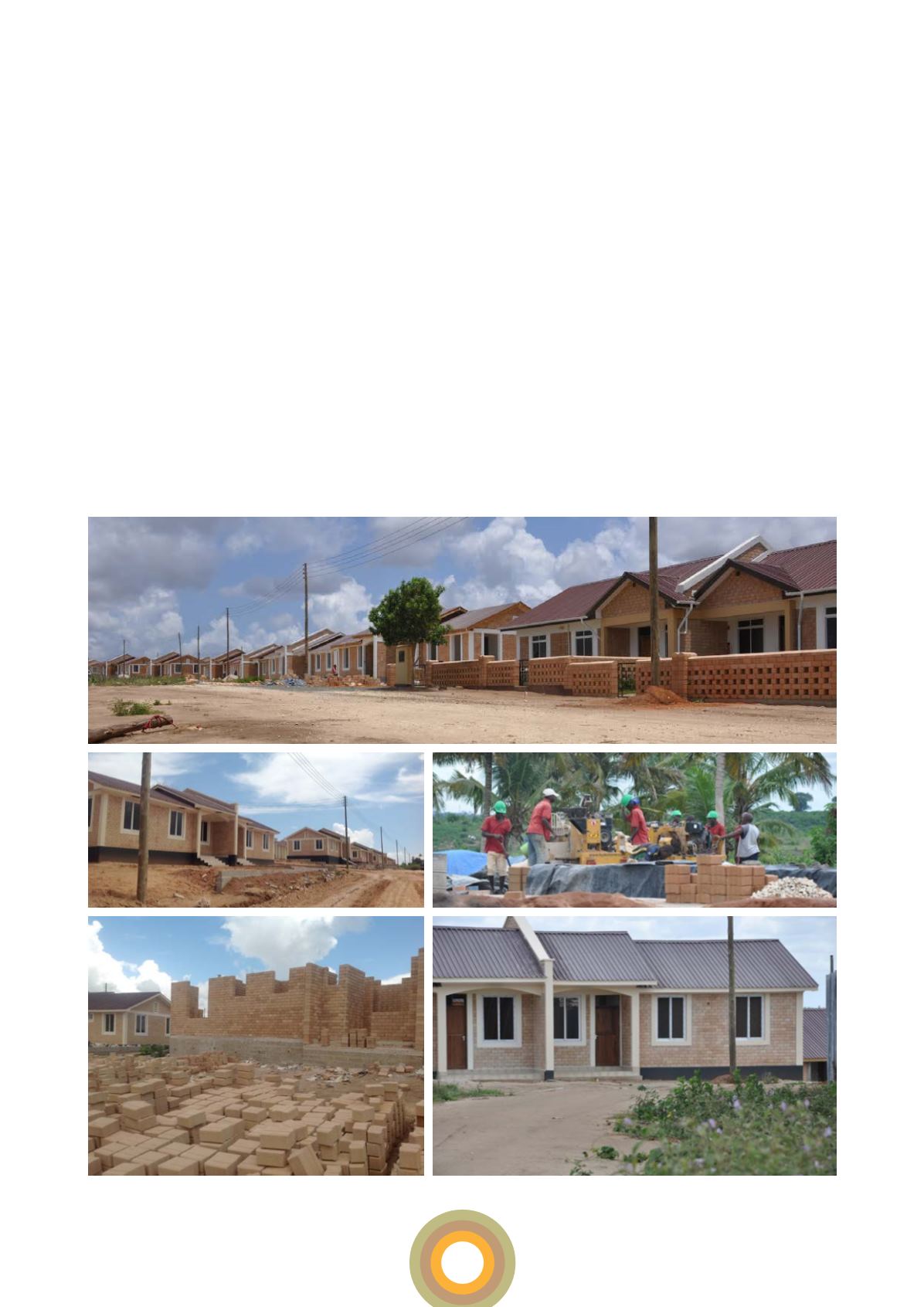
27
Case Study: Tanzania
As part of NHC’s efforts to fulfil its mandate, it
awarded local Hydraform partner Newton Trust the
Kibada project in Dar es Salaam. As a result, some
180 houses have been built using Hydraform
technology at a reported cost savings of 30% on
what would have been the price had conventional
brick and mortar systems been used.
The Kibada project is also the first green housing
project undertaken in Tanzania. Using the Hydraform
system, soil from the local area was used to manufacture
blocks on site. Blocks are cured in the sun rather than
being baked – resulting in significant energy savings
in their manufacture – and producing blocks at the
building site virtually eliminates transport costs (and the
associated fuel emissions) from the equation.
NHC has also used special airflow systems in the
houses to improve cooling, thereby minimising the
energy required for cooling by the inhabitants. Other
benefits include lower construction costs, higher
strengths, faster construction and the creation of
employment around the various sites.
Subsequently, NHC has procured 15 of its own Hydraform
blockmaking machines, each of which can produce 2 000
bricks per day, translating to enough blocks to build a single
85m
2
house every week. The machines have been deployed
at 10 ongoing affordable housing projects.
Delivering
green housing
National Housing Corporation (NHC) Tanzania is responsible
for affordable quality housing delivery in that country.